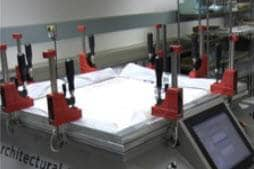
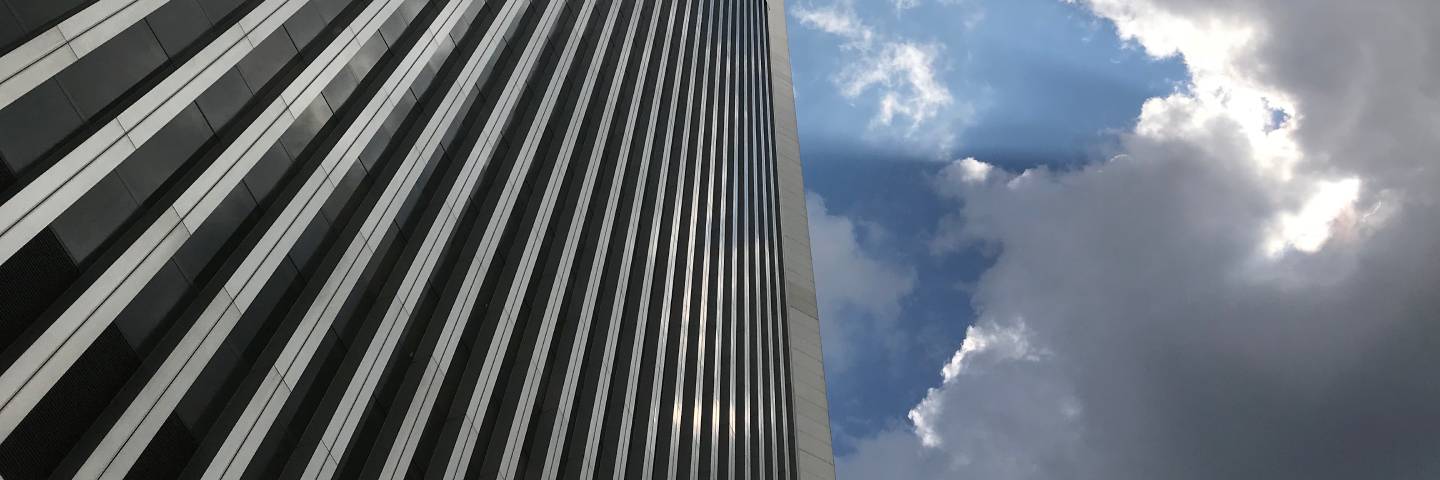
Testing for Airtightness
Proper management of air and vapor in building construction can enhance the longevity of a building, improve indoor air quality, and reduce operating costs by ensuring greater energy efficiency. Building codes increasingly require higher standards for air tightness.
Green building standards, such as USGBC LEED, are structured to maximize levels of airtightness and encourage construction to the highest possible standards. Third-party evaluation for air tightness of materials and assemblies, such as ABAA Evaluation, provides the evidence-based resources necessary to help architects choose products during the design phase that contribute to a whole building system that will meet these standards. The ABAA Evaluation combines the requirements of air barrier material and assembly testing, including energy code requirements and additional material type-specific criteria.
Testing for Airtightness
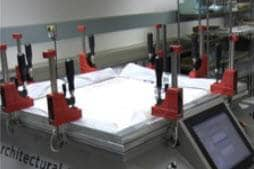
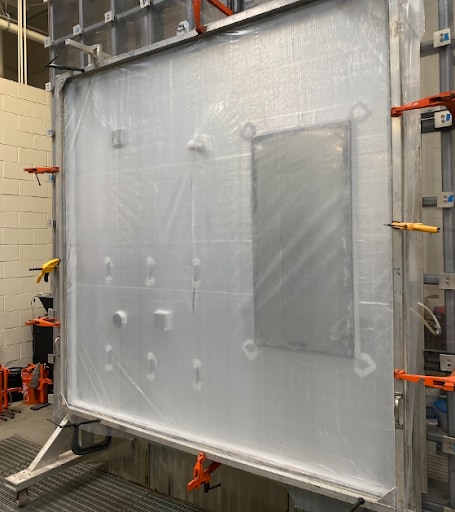
Assembly testing
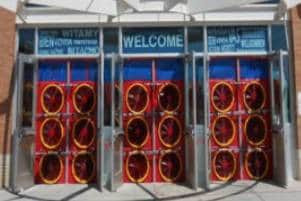
Whole Building Testing
What is a Blower Door Test?
A blower door test measures air leakage rates through a building enclosure under controlled pressurization and depressurization. The test is conducted by an energy professional and is performed according to the following protocol:
- During design, a testing plan is created, communicated, and performance expectations are set.
- The building is prepared for testing by securing all openings, ensuring windows and doors are closed, and turning off all HVAC systems and ventilation fans.
- The fan or series of fans are mounted and calibrated (blower door) into the frame of an exterior doorway.
- The fan pulls create a pressure difference between the interior of the structure and the outside air pressure. The difference in air pressure creates air leakage flows through all unsealed cracks, gaps, and openings, such as wiring penetrations.
- A manometer measures the air moving through the fan in cubic feet per minute at each pressure setting to determine the amount of air needed to replace the leaking air and maintain a constant pressure difference from inside to outside.
- Using the measured air leakage rate and the building's six-sided enclosure surface to determine square footage, they can calculate the ASHRAE 90.1 2022 air leakage target value as 0.35 cfm/sf at a pressure difference of 75pa. A reprint of the full article is available here.
Performance Testing of Water Control Layers - Testing for Water Tightness
Material Testing
Manufacturers use AATCC 127, ICC-ES AC 38 (sheet materials) and AC 212 to evaluate materials for water resistance. However, assembly testing is required to ensure that the interfaces between the various layers provide water resistance.
Assembly Testing
Assembly tests for certifying water resistance include ASTM E331, AC 38, and AC 212. Finally, to ensure that the building will perform as intended by the designer, builders can use in situ testing (ASTM E1105 5.1 – 5.7, AAMA 501.1, and 501.2) to confirm the whole building's water-resistance performance meets the requirements for the project.
Ready to meet with your WALLcontrol Trusted Advisor? Schedule a Meeting