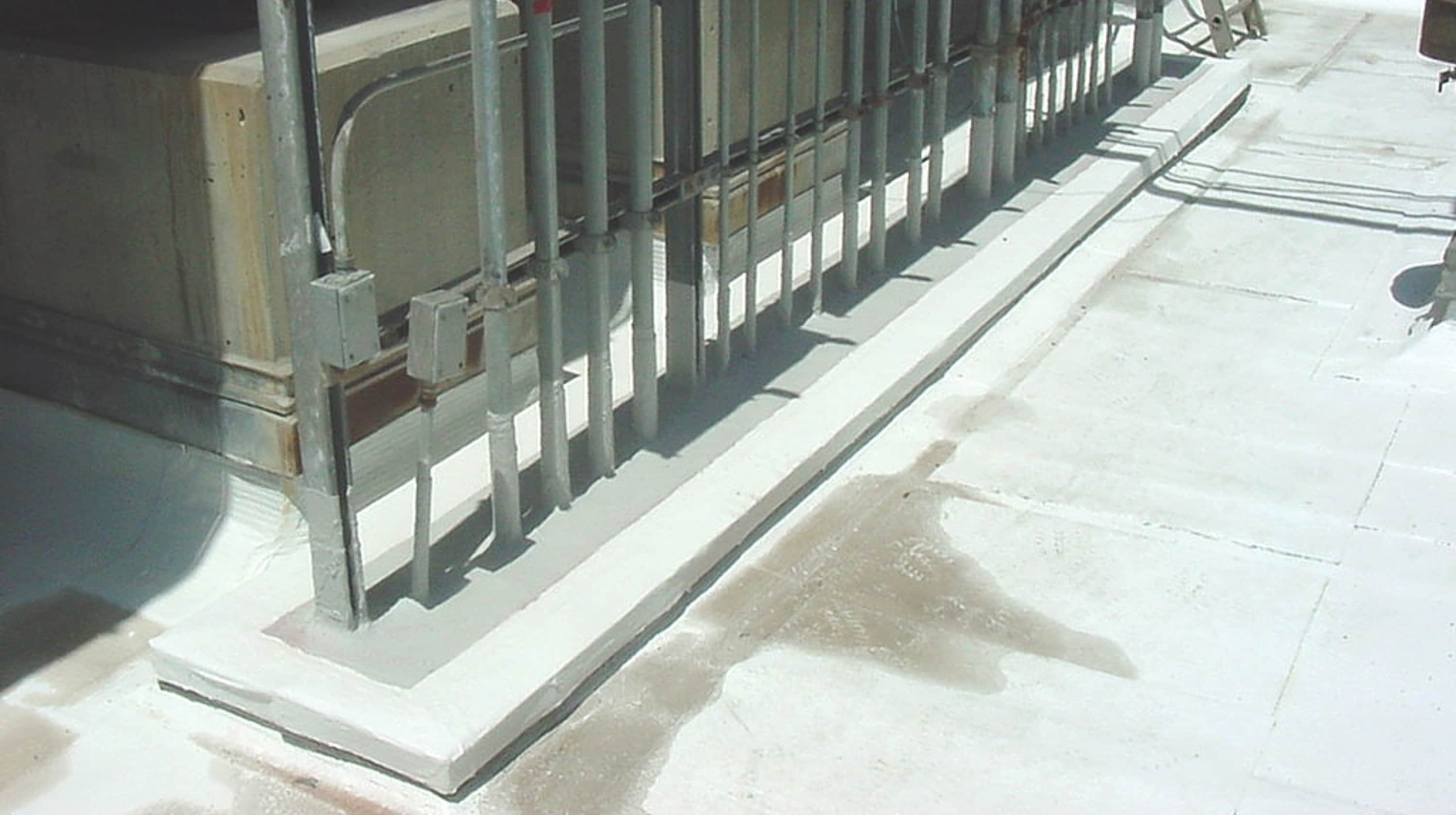
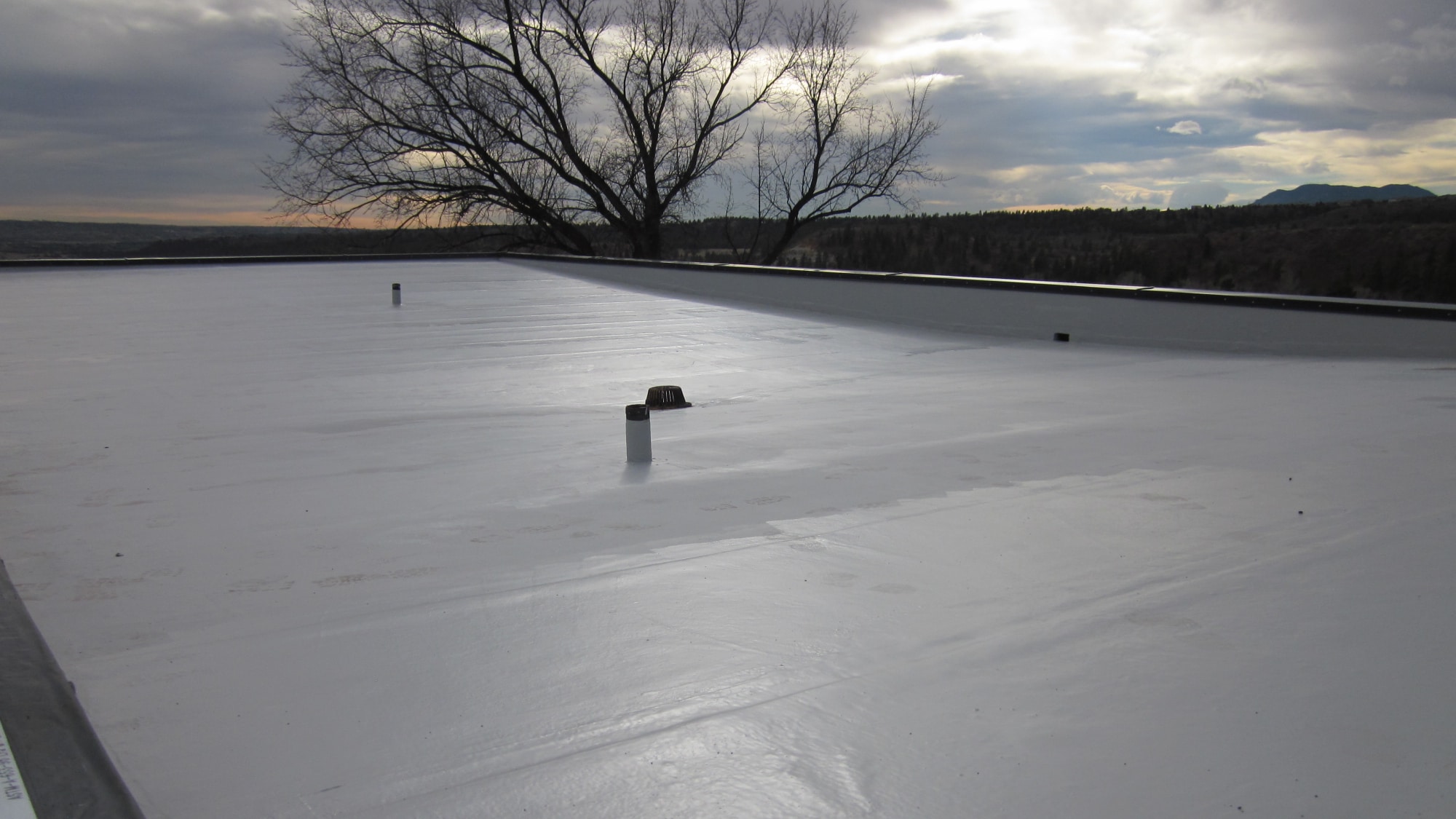
Polymethyl Methacrylate (PMMA) for roofing
Introduction to PMMA
What is PMMA for roofing?
One of the most successful commercial product innovations of the last century occurred in the 1930s when polymethyl methacrylate resins, commonly known as PMMA, were first synthesized. Practical applications for the new resin, which included everything from aircraft windshields to dentures, soon followed. The material proved to be exceptionally durable, and the use of PMMA grew rapidly. But in spite of its outstanding performance, the material was too rigid for use in waterproofing applications - until the 1970s.
That's when a PMMA formulation was developed that, once cured, was resilient rather than rigid. Today, Parapro Roof Membrane and Flashing Systems offer all the benefits of PMMA technology and liquid application in products that meet the performance standards of Siplast.
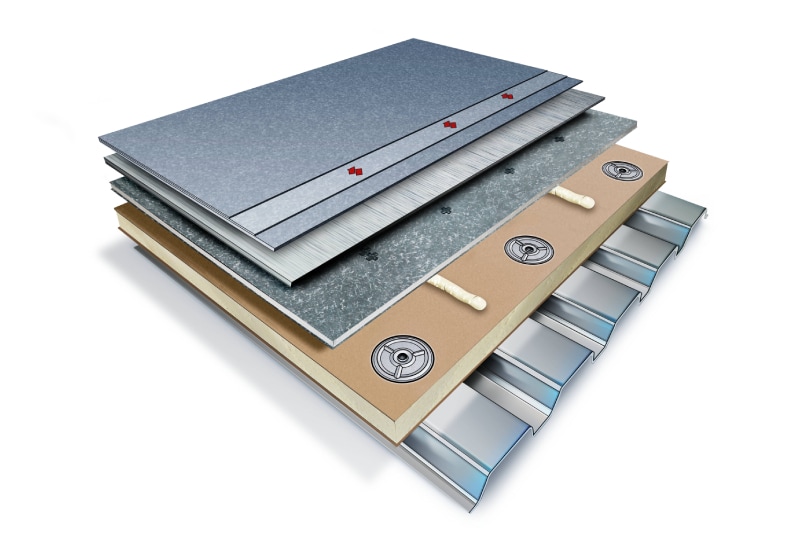
Advantages of Implementing Siplast PMMA Systems
Applications of PMMA for roofing
Flashing details
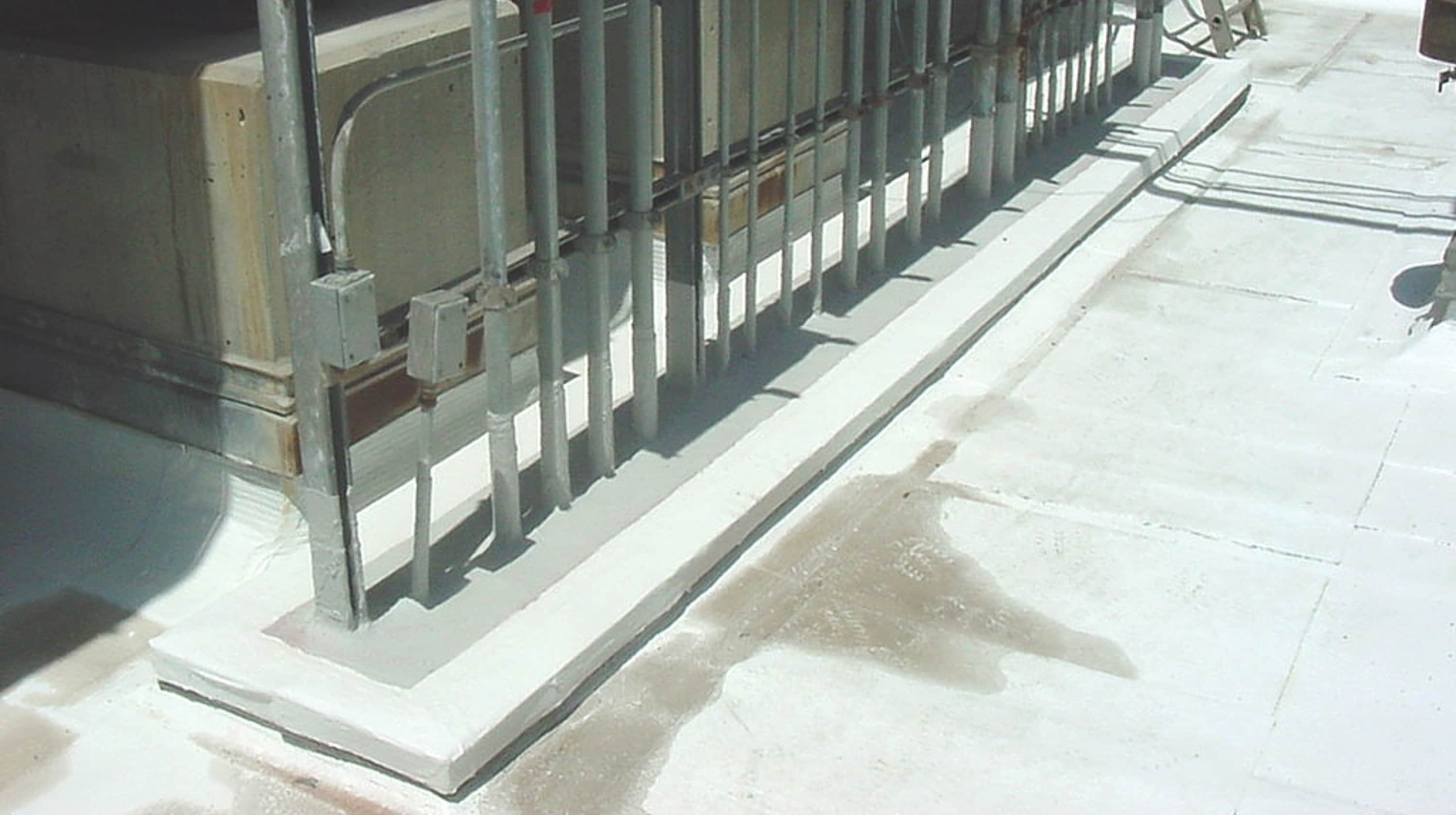
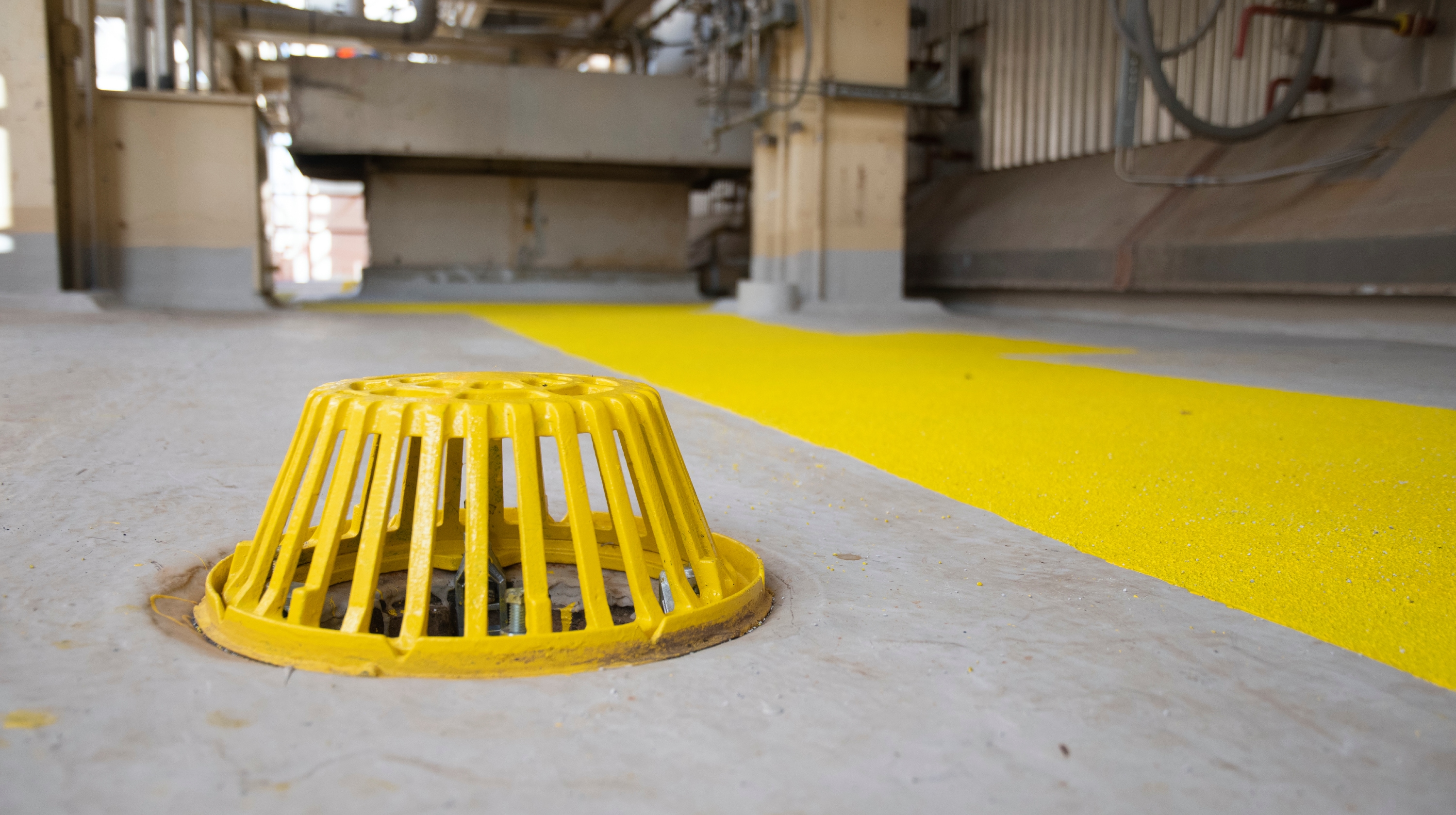
Drain details

Penetration details
Get started with essential components for PMMA roofing
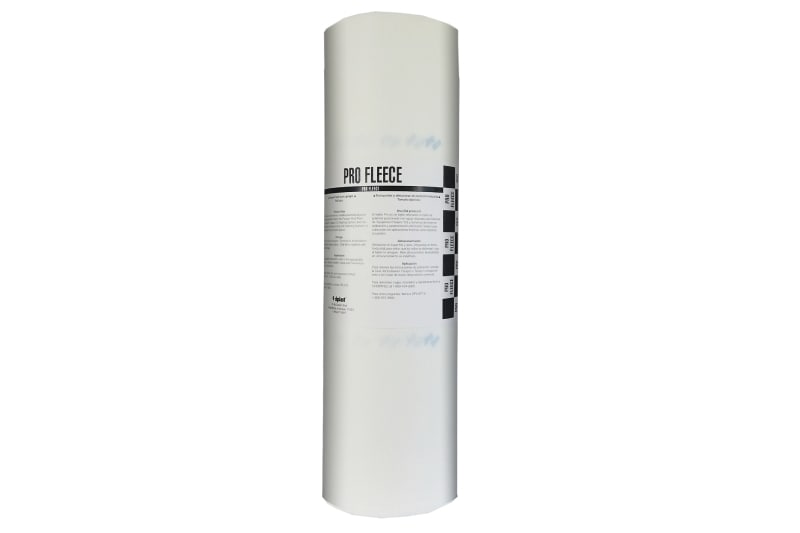
Pro Fleece
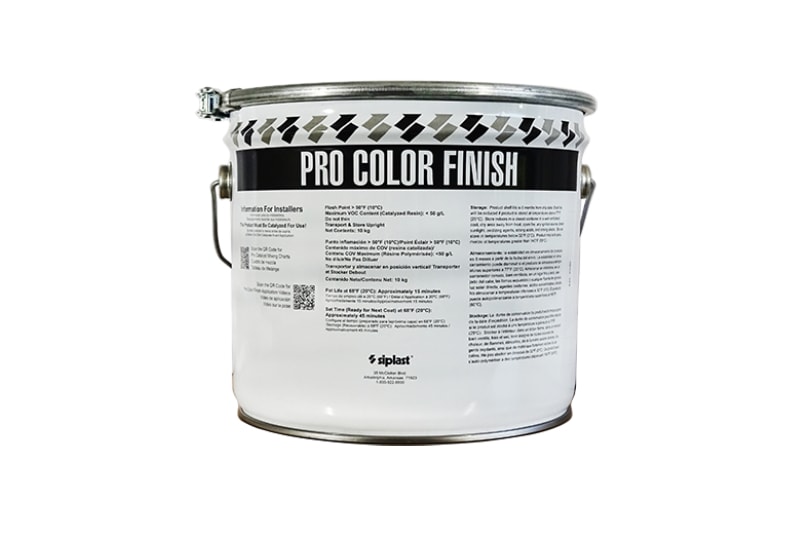
Pro Color Finish
Resins for PMMA roofing

Parapro Roof Membrane Resin for horizontal applications
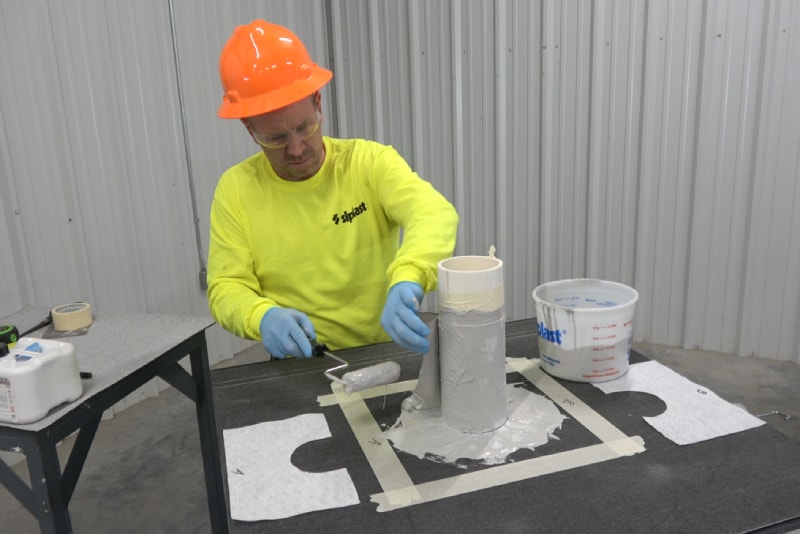
Parapro Flashing Resin for vertical applications
Explore high performance and exceptional protection Discover our systems
Enhance your roof with Pro Base, a component that was made to reflect light
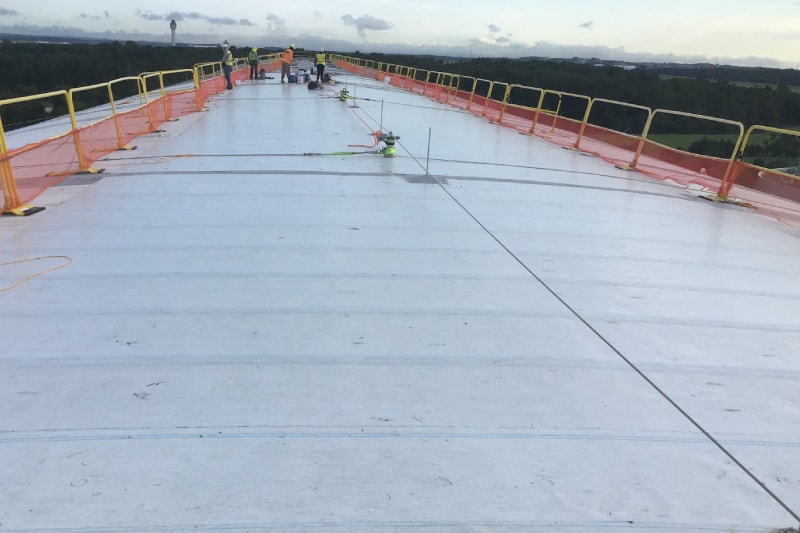
Pro Base series sheets are high-performance
Frequently Asked Questions
What products can I use to clean PMMA roofing systems?
Pro Prep and Pro Prep M are used to clean the transition areas of in-place Parapro and Terapro Waterproofing and Flashing Membranes at tie-ins, repairs, and between staged coats of resin. They are also used to clean metal and plastic surfaces prior to application of Parapro and Terapro Systems. Pro Prep and Pro Prep M can also be utilized for cleaning spills, tools, and equipment.
How to repair damage to PMMA roofing systems?
Avoiding damage to the roof starts with a installation. To help ensure a successful application of Parapro Roof Systems, it's important to remember to accurately catalyze the resins, prepare the substrate, and follow other detailed instructions in the Installer's Guide here.
To prevent damage to cured Parapro Roof Systems, it's helpful to install walkways and surfacing layers on top of the PMMA roofing membrane. The Parapro Roof Systems can be surfaced with aggregates, and optional color finishes can be applied to the cured Parapro Roof Membrane, simplifying the application and maintenance of rooftop markings.
In the case of a recover, Siplast materials are especially suitable and widely used in these roofing applications. Each re‑cover application is unique and should be considered individually. Siplast recommends the use of analytical tools such as nondestructive moisture survey methods as well as test cuts and any other evaluation methods available to ascertain existing roof conditions.
This thorough inspection of the existing roof conditions must be made to determine that:
- the deck is structurally sound,
- the deck is able to take the added weight of the new assembly,
- areas where moisture may be present have been located,
- the method and degree of attachment of the existing assembly has been specifically ascertained,
- minimum 8‑inch flashing heights will exist at curbs, walls, etc, and
- the new assembly will provide proper drainage.
In all cases, the old roof assembly should be separated from the new Siplast materials with a product and installation procedure appropriate to the existing deck, roof system, and surfacing. Please contact your Siplast Representative for recommendations tailored to meet your particular roof re‑cover conditions.
Proper storage of PMMA Materials
To facilitate the application of adhesive at ambient temperatures below 70ºF (21ºC), all materials such as resins, adhesive, and roll goods should be stored in a warm place such as a heated trailer or other climate-controlled storage area prior to use.
Application in cool weather can be completed more effectively by cutting warmed rolls into halves or thirds and stacking the sheets with the unsurfaced-side upward to allow for solar heating. Cut sheets should be allowed to lay flat for a minimum of 30 minutes (time will vary based on the ambient temperature and solar load) to allow them to “relax.”
For additional information see Cold Weather Application SBS & PMMA Products.