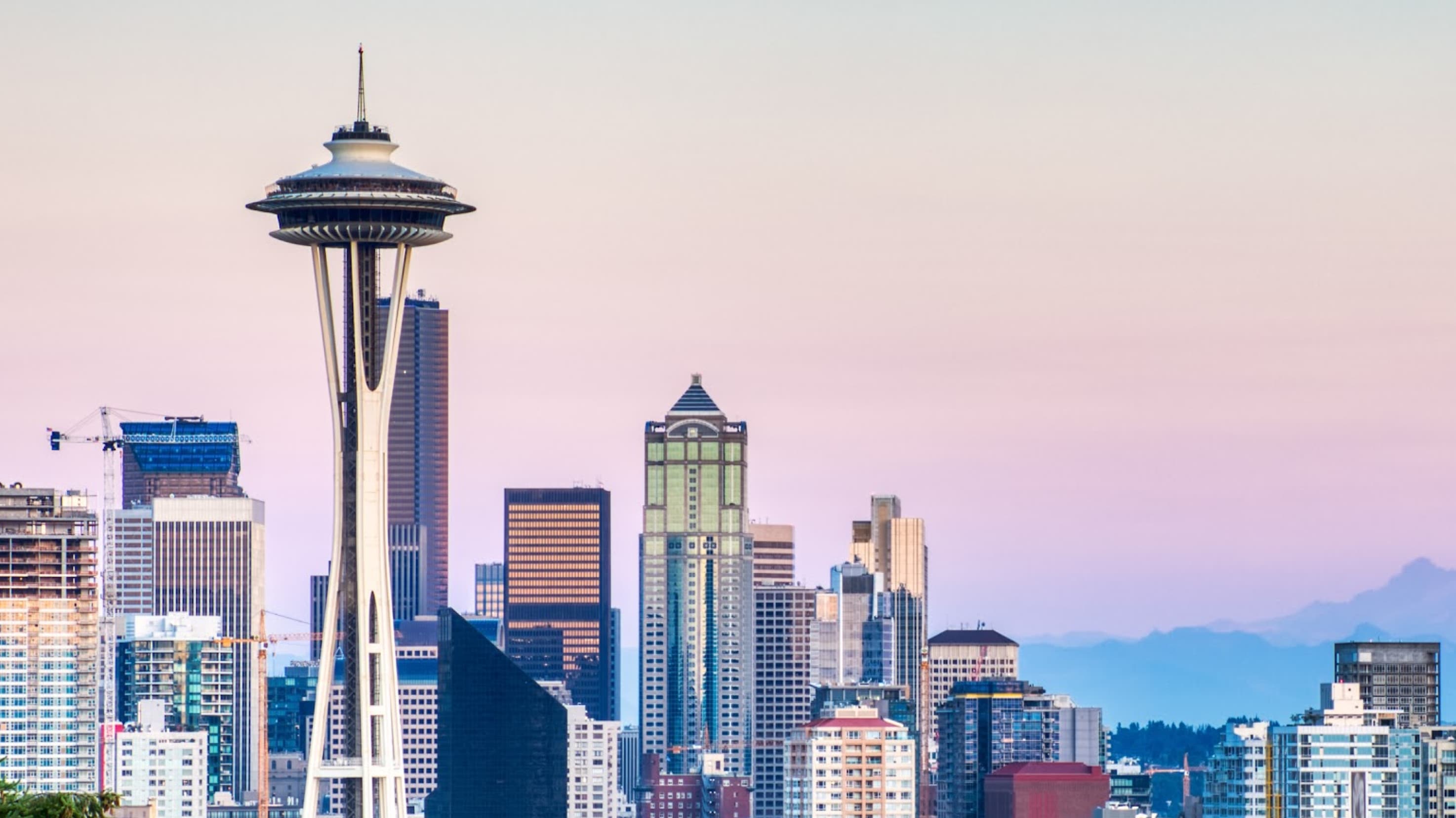
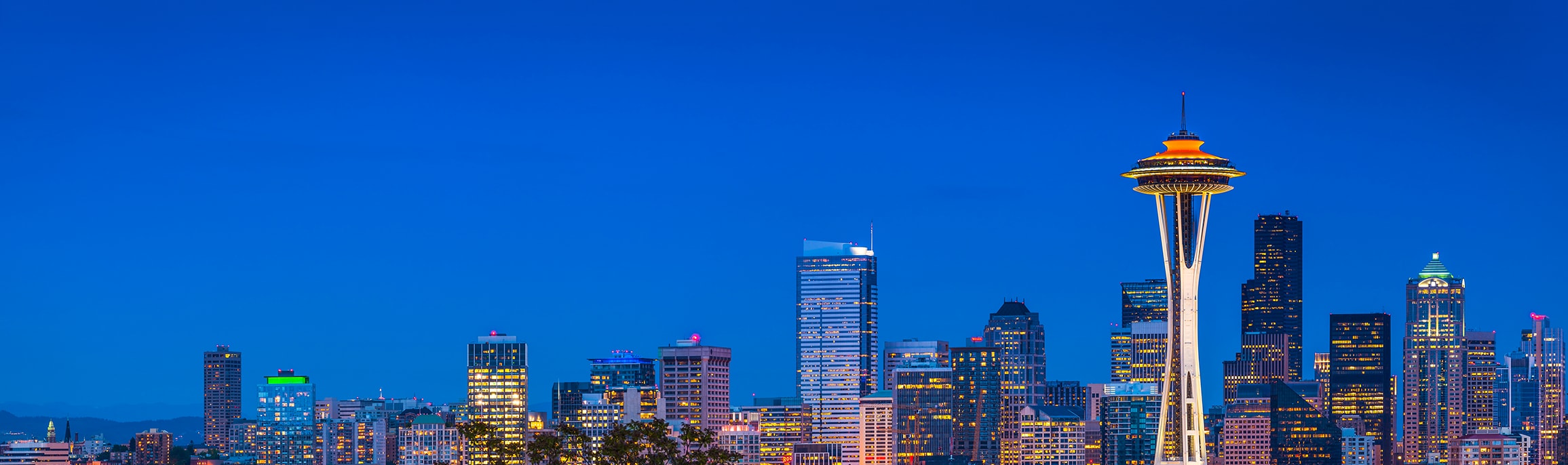
Polymethyl Methacrylate (PMMA) for waterproofing
Introduction to PMMA
What is PMMA for waterproofing?
One of the most successful commercial product innovations of the last century occurred in the 1930s when polymethyl methacrylate resins, commonly known as PMMA, were first synthesized. Practical applications for the new resin soon followed, but the material was to rigid for use in waterproofing applications - until the 1970s. That's when a PMMA formulation was developed that, once cured, was resilient rather than rigid. Today, Terapro Waterproofing and Surfacing Systems offer all the benefits of PMMA technology in products that meet the performance standards of Siplast.
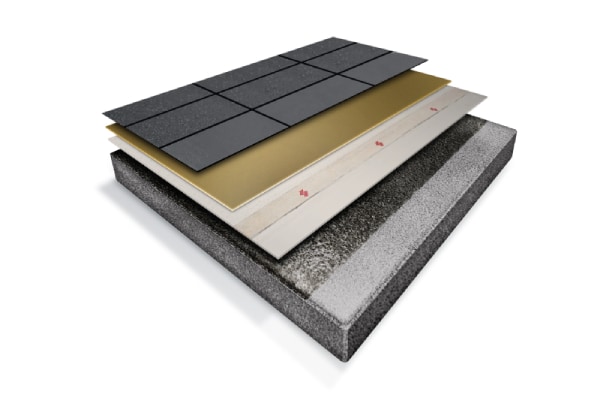
Advantages of Implementing Siplast PMMA Waterproofing Systems
Waterproofing applications benefit from the numerous advantages PMMA resins hold over other liquid-applied waterproofing systems. Terapro Resins are VOC compliant, and unlike many polyurethane materials, are solvent-free, and isocyanate-free. Terapro Systems provide exceptional:
- Abrasion resistance.
- Weather resistance.
- UV resistance.
- Durability.
Applications of PMMA for waterproofing
Project profiles
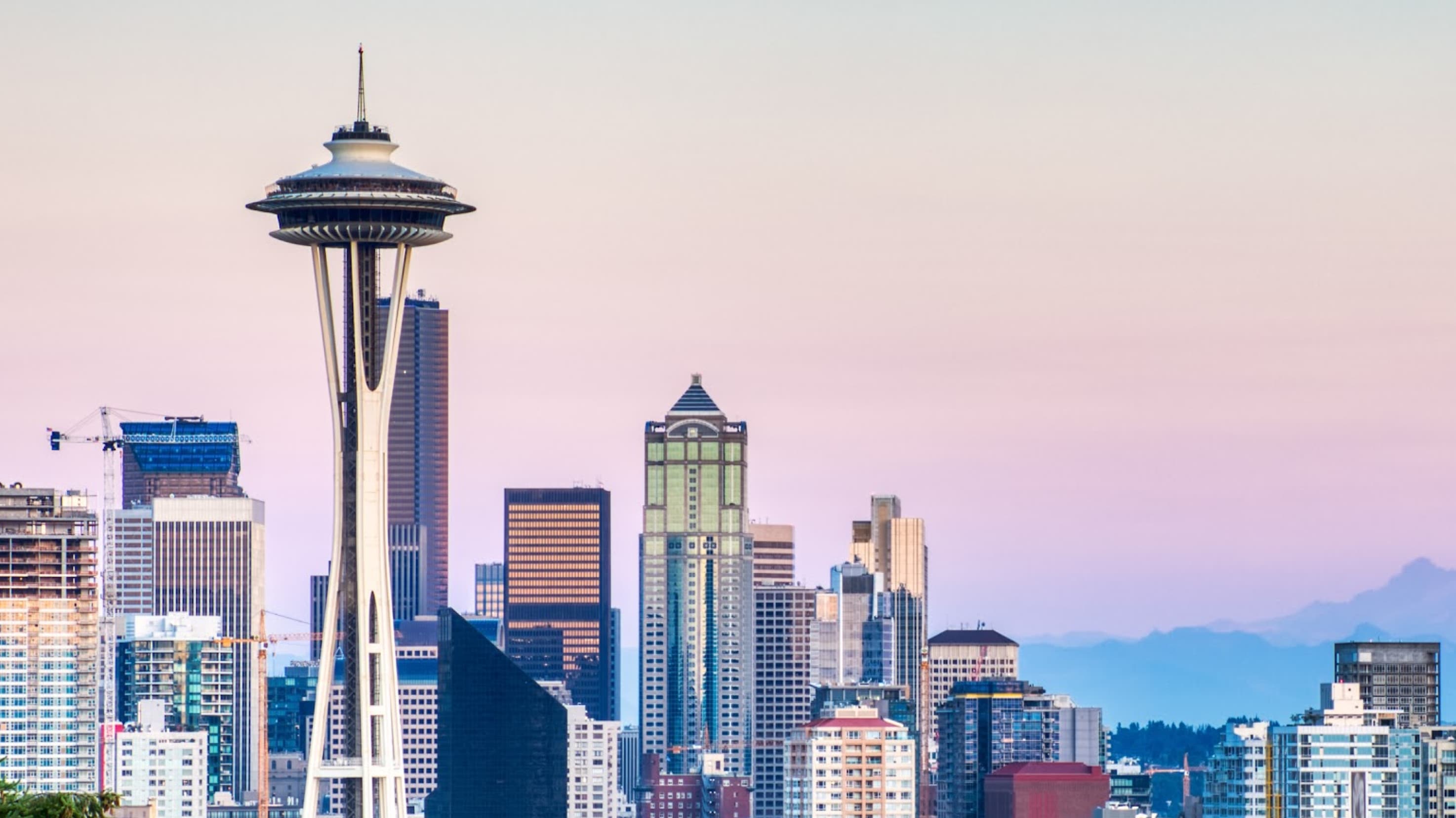
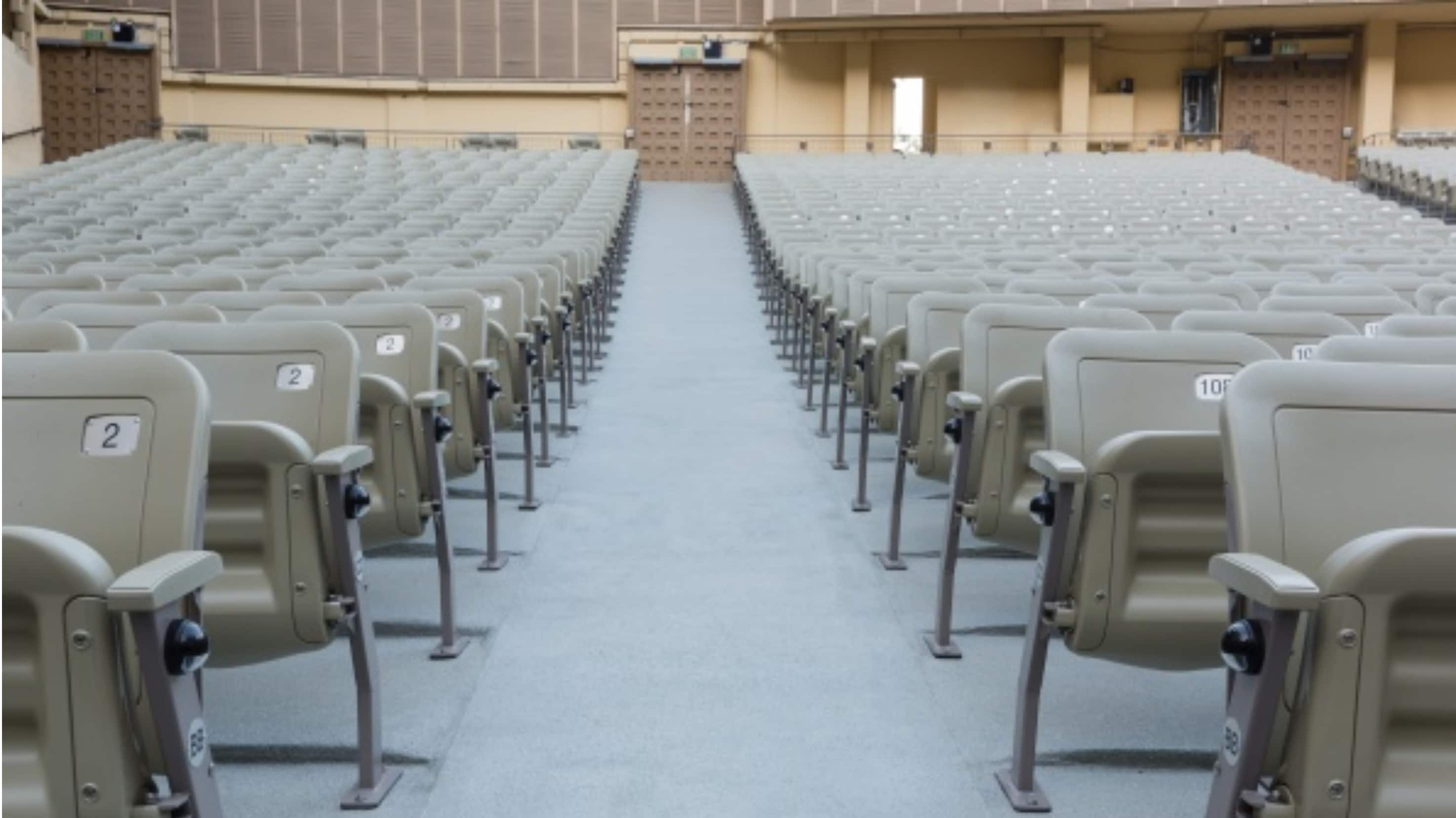
The Ford
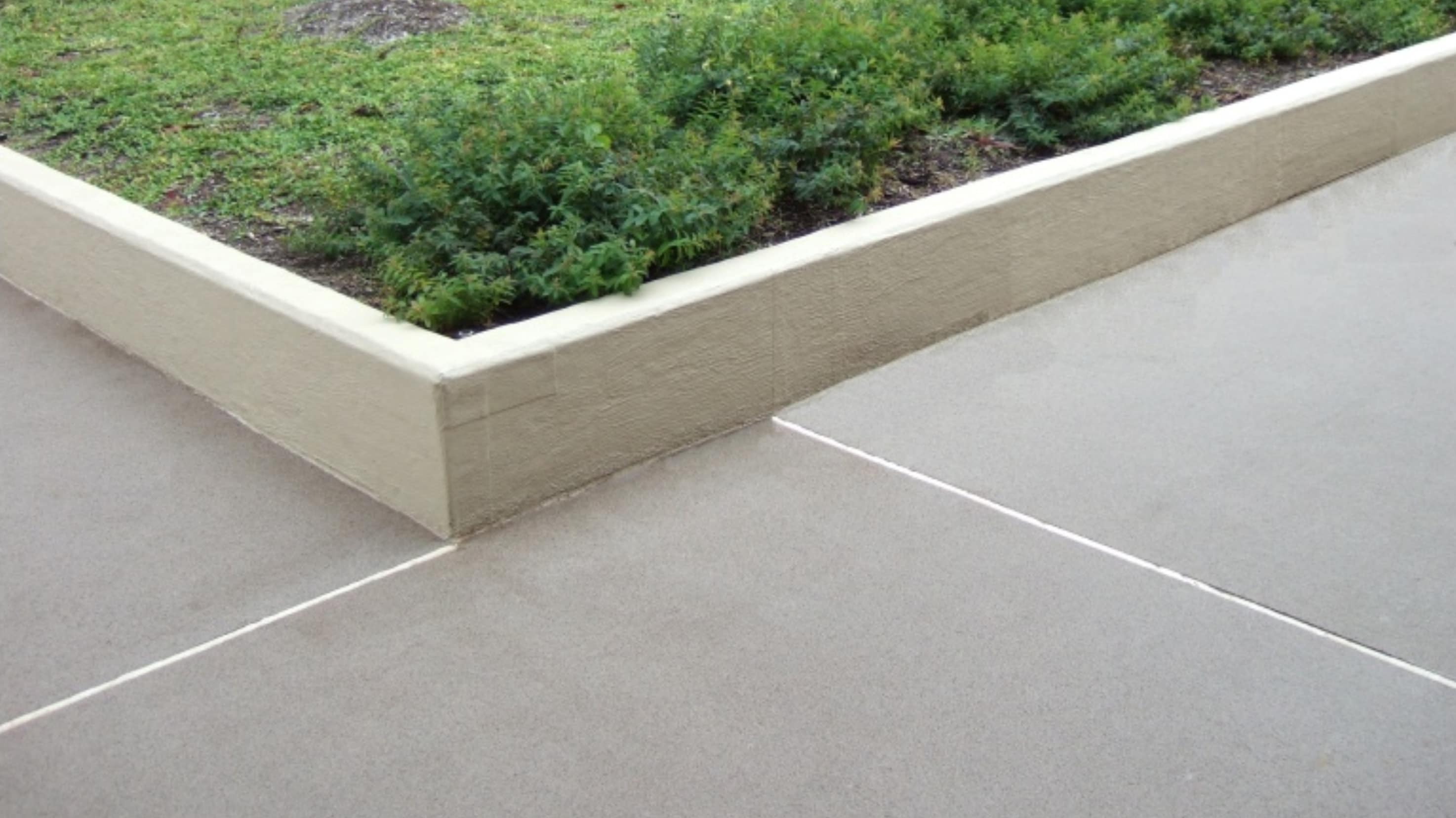
Circle Towers
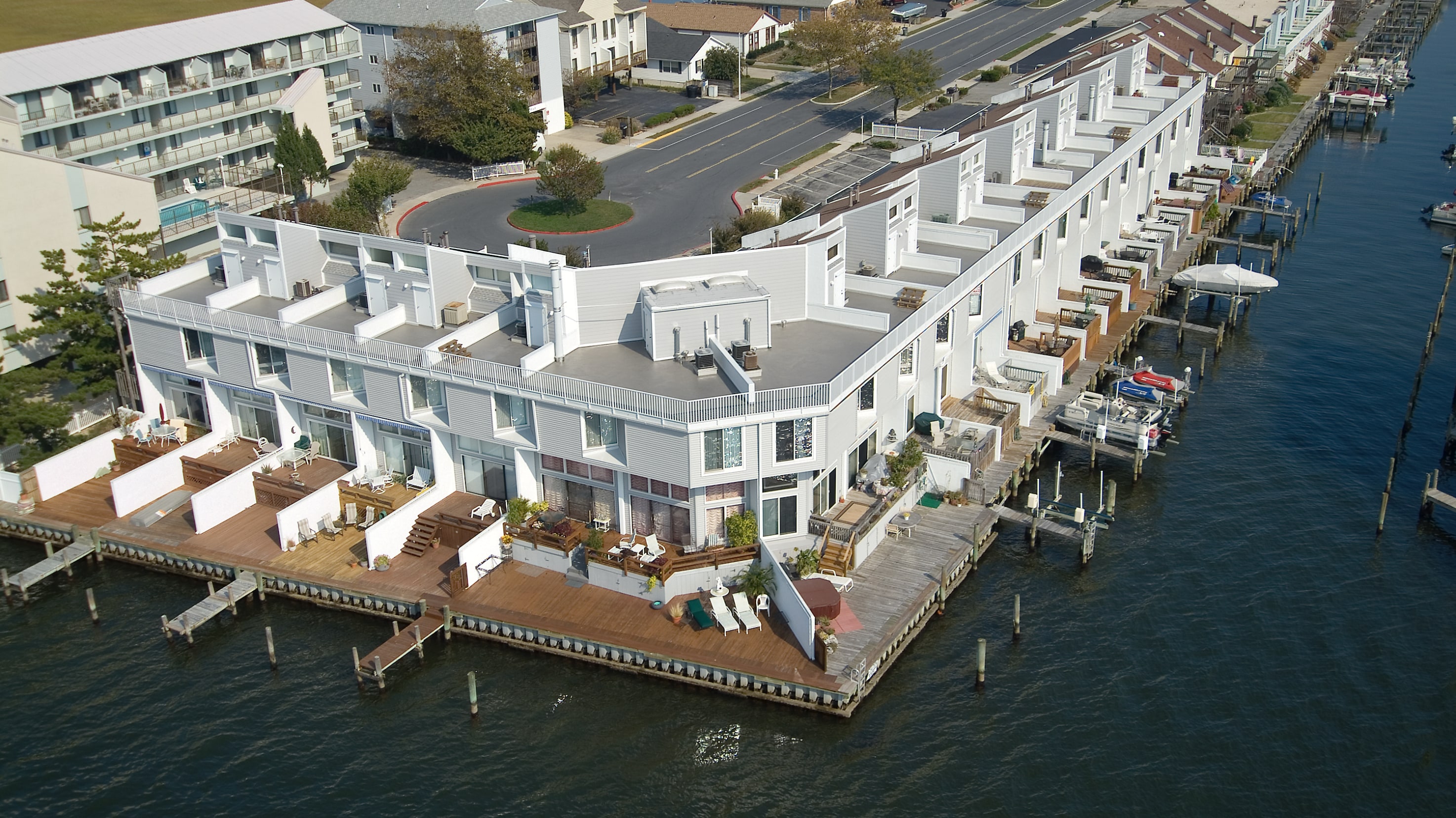
Deer Point
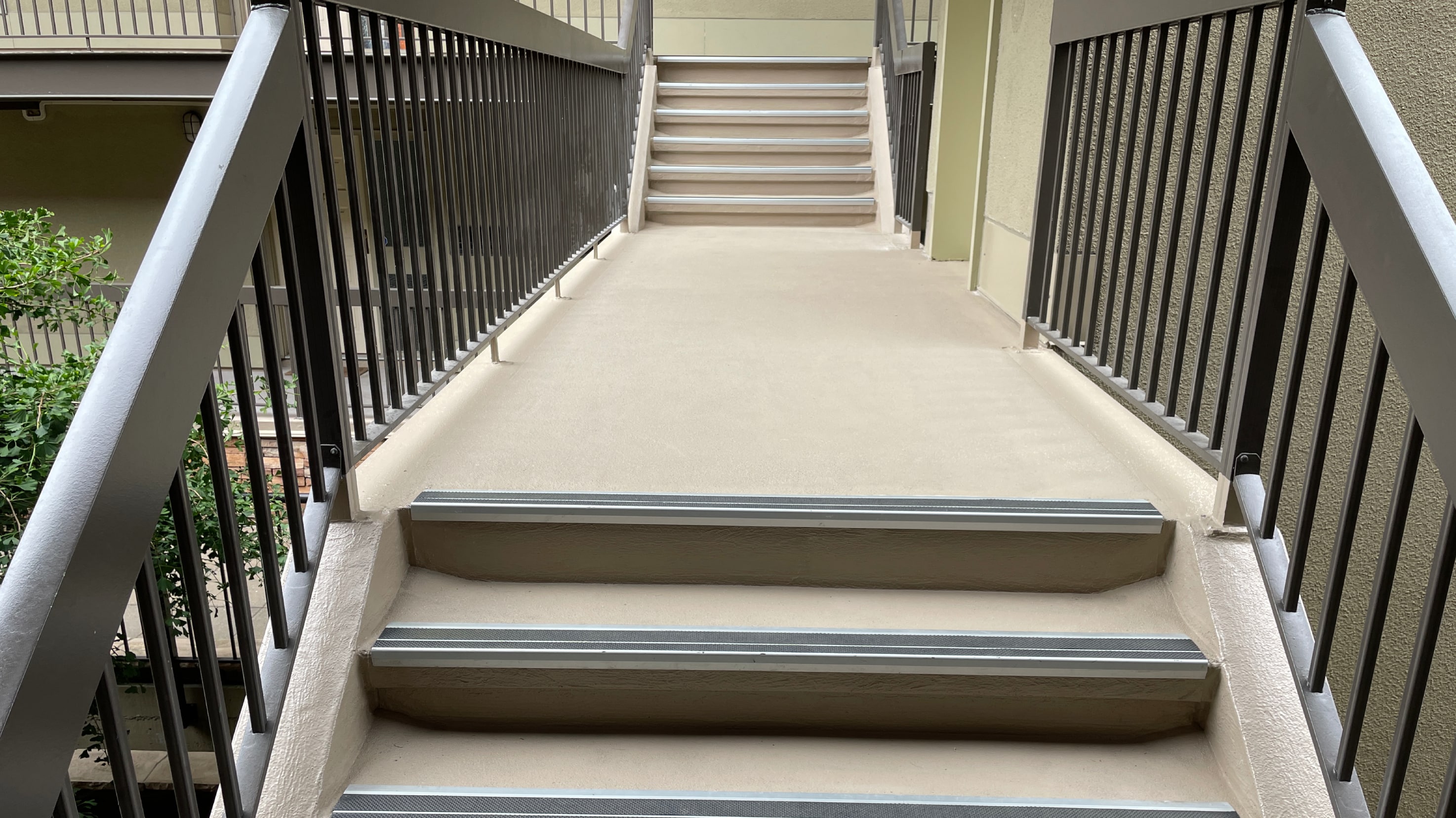
Harbourside Terrace
Get started with essential components for PMMA waterproofing
Reinforcement
Resins for PMMA waterproofing
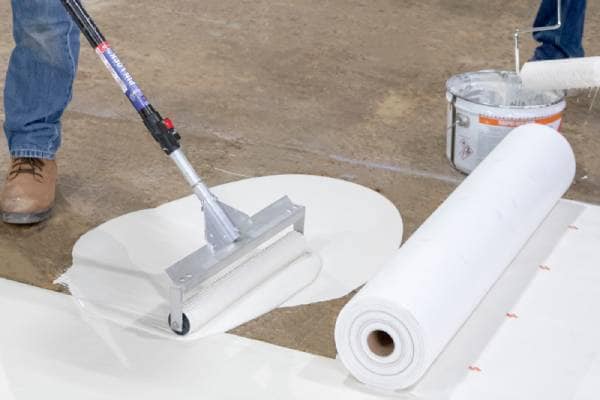
Terapro Base Resin for horizontal applications
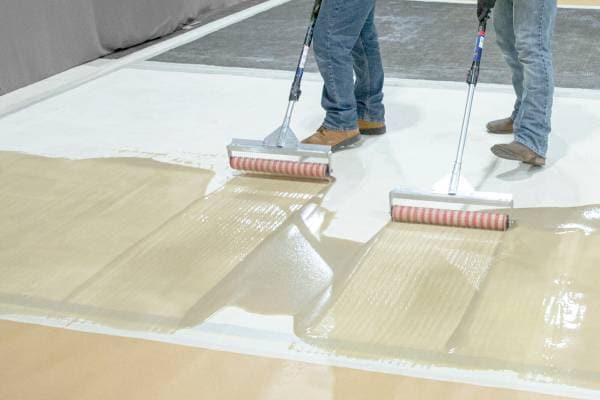
Terapro VTS Resin for horizontal vehicular applications
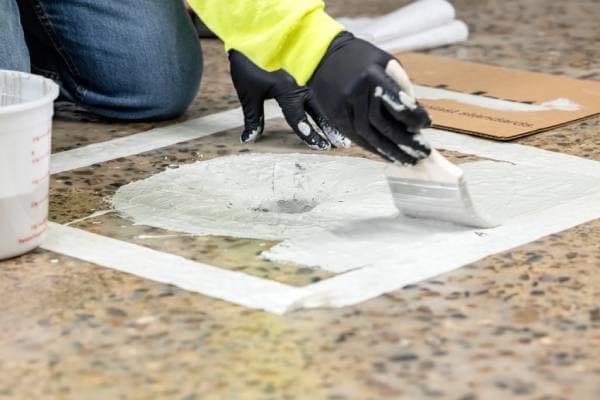
Terapro Flashing Resin for vertical applications
Explore high performance and exceptional protection Discover our systems
Enhance with accessories for PMMA waterproofing
Frequently Asked Questions
What products can I use to clean PMMA waterproofing systems?
Pro Prep and Pro Prep M are used to clean the transition areas of in-place Terapro Waterproofing and Flashing Membranes at tie-ins, repairs, and between staged coats of resin. They are also used to clean metal and plastic surfaces prior to application of Terapro Systems. Pro Prep products can also be utilized for cleaning spills, tools, and equipment.
How do I ensure successful application of liquid-applied waterproofing systems?
With multiple components in a waterproofing system, there is a higher risk of system failure and water infiltration. Here are some helpful tips for working with the Terapro Waterproofing and Surfacing Systems:
- Terapro is a two-component product. All Terapro Resins, both summer and winter grades, must be catalyzed prior to application regardless of ambient or substrate temperature. Because Terapro Resins are not activated until they are mixed with Pro Catalyst, contractors can eliminate waste by only preparing the amount of resin required for a job. Uncatalyzed resin will not cure, and will result in a failed application.
- Properly prepare the substrate and keep the application site clear of debris. Contamination of Terapro materials during storage, mixing, and application can adversely affect the system's performance.
- Always follow the detailed Terapro application instructions in the Terapro Waterproofing and Surfacing Systems Installer's Guides here.
What is proper storage and handling of PMMA waterproofing materials?
Warm weather presents a unique challenge to the storage and handling of PMMA materials. Always store PMMA resins and catalyst products out of direct exposure to sunlight and areas where solar load can be excessive (such as vehicle dashboards). PMMA resins and catalyst products should be stored in cool, dry places that are well ventilated. These materials should never be stored on the job site, so keep PMMA resins and catalyst products away from direct sunlight until application. Materials kept on the job site during application should be placed on a pallet in a shaded, well-ventilated area. In unshaded areas, materials should be covered with a white, reflective tarp in a manner that allows air circulation underneath the tarp. Refer to the safety data sheets here for these materials for detailed handling and storage information.